If customers can afford the price, I can manage the quality as they do!When we talked about the quality management of XX factory, my friend said to me. The implication is that the poor quality of color boxes is due to the low price offered by customers. If words are not opportunistic, I can only be silent.A factory shipped 3000 boxes, there were 400 spare parts. Finally, the customer finished the inspection, and the number of good products was less than 3000. The discerning eye sees at least two problems here,1. In order to ensure the quantity of good products, 400 more were printed, which were wasted;2. In order to save costs, the company gave up the delivery inspection, resulting in a large number of defective products outflow, the company's reputation loss.Obviously, in the boss's consciousness, the above two losses are ignored, because the enhancement of quality management will increase the cost. On the contrary, improving the quality management level will not increase the cost of enterprise management, but will help to reduce the waste in production.Good quality management is actually very simple.1. First sample confirmation.The first sample is different from the customer signed sample, the purpose of which is to provide standards for production and avoid disputes over delivery; The first sample is the first product in batch production, which must be checked strictly according to the sample signed by the customer. More and more enterprises are aware of the importance of the first sample confirmation, the first sample inspection is the most important measure to avoid mass production defects! If the first sample is wrong, the whole batch of color boxes will be scrapped.
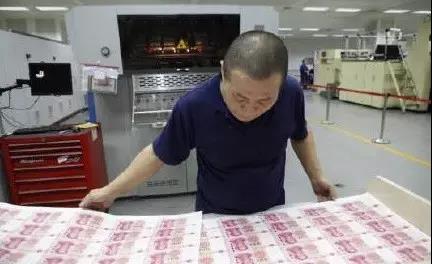
2. Regular sampling inspection during operation.In order to prevent the change of production conditions in the process of operation, which leads to bad, the most effective method is regular sampling inspection. The spot check in printing can adjust the color change, ink failure, and even stop processing to prevent batch defects. There is a packaging factory, delivery to the customer was found a large number of poor sticky box, overflow, bell mouth and so on; Back to the production line, we found that the employees were very skilled and the speed of gluing boxes was very fast. However, no one ever took the spot check and did not have their own regular inspection. Everyone was working hard. The employees did not know whether there were defective products or not, and the management personnel did not know. It's strange that this mode of production can produce good quality products.
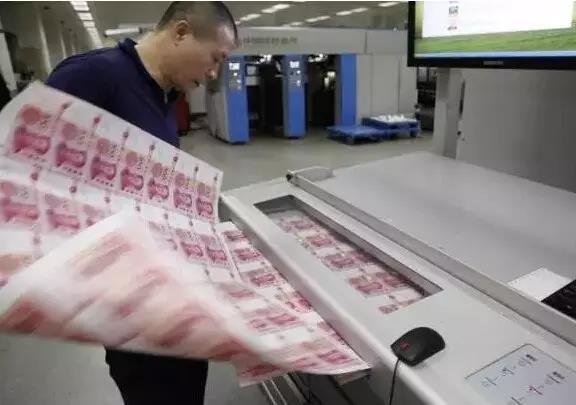
The above two inspections are the focus of production quality management and inspection in the production process. If there is no first sample confirmation and sampling inspection in the process of operation, problems can not be found in the operation. If we reflect on the operation mode, improve the production environment and maintain the equipment status, we can not produce qualified products. For small printing plants, it is not even necessary to add special quality inspection personnel, only need to add the first sample confirmation, operation sampling and strict implementation in the procedure. Not only will not increase the management cost as we think, on the contrary, it will greatly reduce the quality risk and improve the yield.
"Products are produced, not checked out!" that is to say, delivery inspection, which is actually a measure to make up for the lost sheep, so as to avoid the bad products flowing into the customers and causing credit loss.The key to quality lies in the consciousness of the boss. Big problem, big problem, it's not hard to get rid of the boss!